Applying a manufacturing mindset in the water industry to tackle its biggest challenges
Published: 21 August 2024
It is widely acknowledged that water companies and the sector in general need to do more to collaborate and share ideas from within and outside the sector. Much has been done to improve this position in recent years and more is needed. AMP8 will be the largest asset management plan in the sector’s history. We need to be brave and ambitious in our efforts, but also consider a fundamental shift in our usual approaches.
Director Commercial and Customer Programmes, Emma Carroll-Walsh, led a manufacturing mindset in her previous role as Director of Built Environment in water, construction, and linear infrastructure such as road and rail, taking a lead on innovative project management programmes. Let’s look at what it would take to establish a manufacturing mindset in the water sector.
What are the key challenges in the water sector?
The water sector has three key priorities for AMP8:
- Maintain the highest quality drinking water for a growing population
- Ensure the security of our water supply in the future
- Significantly reduce the amount of sewage entering rivers and seas
Water companies’ AMP8 business plans are ambitious, including:
- Build ten new reservoirs to secure our water supplies
- Cut leakage by over a quarter by 2030 compared with the start of the decade, which will increase performance to among the top five countries in Europe
- Invest £11 billion to reduce overflow spills – more than triple the current rate and representing the most ambitious modernisation of sewers since the Victorian era. Spills are forecast to reduce by more than 140,000 each year by the end of the decade, thanks to upgrades of sewage works, the creation of new nature-based schemes to manage rainwater and technology to better manage flows
- Install advanced technology at sewage works to remove over a million tonnes of phosphorus from rivers
What is a manufacturing mindset?
A manufacturing mindset focuses on efficiency and standardisation in production processes to maximise output and minimise costs. IKEA exemplifies this approach by producing only one or two types of dowels, door components, and side panels, which can then be utilised across a multitude of products. This streamlined method reduces variability and simplifies the manufacturing process, leading to cost savings and enhanced productivity.
The Product Platform Rulebook is an open-access guide to support industry, including clients, consultants, contractors, manufacturers and product suppliers, in building capability and capacity to develop and deploy product platforms to meet demand.
However, for a manufacturing mindset to be truly effective across the entire sector, it must adopt a collaborative approach. This involves integrating efforts and knowledge across different teams and stakeholders to ensure consistency, share best practices, and foster innovation. Collaborative efforts enable a unified strategy that can address challenges more effectively, optimise resource usage, and ultimately drive the entire manufacturing industry towards greater efficiency and effectiveness.
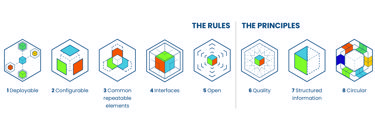
Why is the current model broken?
One major problem is the industry's nervousness to adopt new methods without established standards, leading to a reluctance for innovation and maintaining a closed mindset. This hampers progress and limits improvements in efficiency and productivity. The supply chain also faces significant constraints, such as a shortage of suppliers and resources (people and raw materials, e.g. steel and concrete). This issue becomes glaringly evident when considering large-scale projects like building new water treatment plants. Without applying a manufacturing mindset to construction sites, these projects cannot be delivered effectively.
The upcoming AMP8 promises further strain on the already limited supply chain, as it adds demands on top of existing national need for hospitals, housing, remediation, and maintenance of current infrastructure. Viewing AMP8 in isolation from the broader UK infrastructure demands ensures that delivery is unattainable.
Traditional construction methods exacerbate wastefulness, with materials being moved up to seven times before reaching their destination, and for every four houses built, enough waste is generated to build a fifth. Continuing with outdated methods ensures nothing changes, perpetuating inefficiency and waste. Adopting a collaborative manufacturing mindset across all sectors is essential to address these challenges and build a more sustainable future.
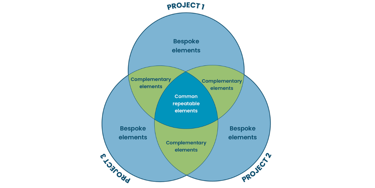
Applying a manufacturing mindset to the water sector
Applying a manufacturing mindset to the water sector involves identifying key assets for standardisation and exploring supply chains beyond traditional boundaries. By focusing on standardising critical components, the water sector can achieve greater efficiency and consistency in operations.
AMP8 regulatory drivers offer a prime opportunity for standardisation, particularly in nature-based and blue-green solutions. This potential can be unlocked through the industry's asset standards and a design for manufacture and assembly (DFMA) approach during all stages of project development – feasibility, optioneering, concept, and detailed design.
For example, the adoption of laser-cut reinforcement over traditional rebar can significantly reduce material wastage while enhancing on-site safety, in addition to reducing on-site labour requirements. This not only improves safety, but also facilitates a transition to a manufacturing environment, necessitating retraining and upskilling of the workforce. This massive upskilling effort is crucial for equipping workers with the skills needed in a more industrialised setting.
Embracing these changes can transform the water sector, making it more resilient, efficient, and capable of meeting future demands. By integrating a manufacturing mindset, the sector can overcome current limitations, optimise resources, and contribute to sustainable infrastructure development.
A manufacturing mindset is only part of the solution; it isn’t the only solution
While adopting a manufacturing mindset is crucial for enhancing efficiency and standardisation in the water sector, it is only part of the solution; collaboration across the industry is equally essential.
Engaging stakeholders, sharing best practices, and integrating efforts can drive innovation and address supply chain challenges. Additionally, investing in workforce training, adopting advanced technologies, and implementing sustainable practices are vital components.
Together, these elements can create a holistic approach that not only improves productivity, but also ensures resilience and sustainability in the sector, leading to more effective and comprehensive solutions.
Latest resources
- Insights
Assuring the future: Navigating AMP8 with confidence in technical assurance
- Insights
Summarising the CMA's redetermination approach
- Insights
Raising the bar for asset management in the water sector: Ofwat’s asset maturity consultation
- Insights
The future of asset management is nature-positive — are you ready?
Here to solve your biggest challenges and grow sustainable value
Our expert consultants are available to broaden your thinking, lead transformation, and help you achieve successful outcomes.
Contact our experts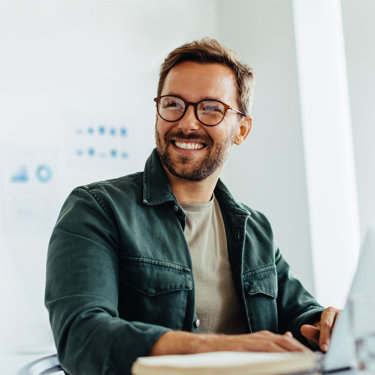